Tarkashi Inlay is a highly skilled art form that is more than 500 years old. Traditionally, the local artisans on the Eastern shores of Odisha practice it. As the name suggests, Tarkashi is the technique where thin strips of wire are engraved on the surface of the wood.
Tarkashi Inlay is believed to have come from Mainpuri, Uttar Pradesh. The craft was patronized by the royals of Jaipur and Amber. Sawai Jai Singh, during his regime, invited Sri Sarwan Lal Misra a master craftsman from Mainpuri who started practicing and teaching this craft in Jaipur. Few people learnt the craft and carried the tradition forward.
At present there are about four families and fifteen individuals practicing this craft in Jaipur. These families are well regarded and belong to the Jangid community. They are supposed to deal with wood. These skills are transferred to the younger generation by the elders. Mohan Lal Sharma is an inhabitant of Jaipur who practices Tarkashi Inlay for over 40 years now! Book a masterclass with here!
Jaipur is the storehouse of various arts and crafts, especially metal crafts. Metal was an embellishment owned and used by the royals. A number of crafts became patronized. The royals due to their artistic uniqueness and magnificent work demonstrated by the craftsmen
The Process Of Making Tarkashi Inlay
Tarkashi is an intricate art form. It comprises of many steps. Let us undertsand them here:
1. Seasoning of the wood
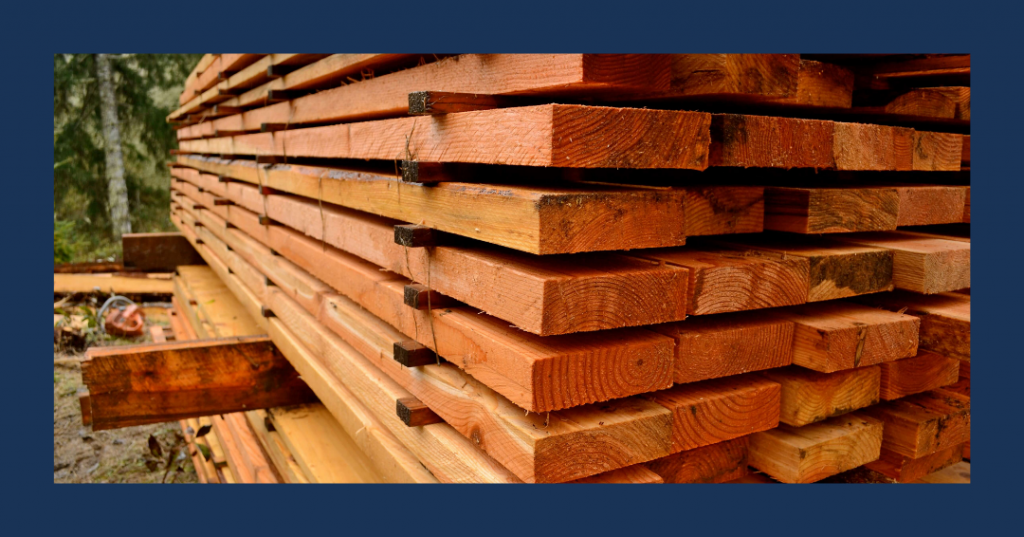
This process ensures that the moisture is removed from the woodcut. A block of fresh wood is dried or seasoned for better Tarkashi. This involves the wood being stacked between two planks. There is enough space for air to pass. The longer the seasoning, the better the wood gets.
2. Cutting of the wood
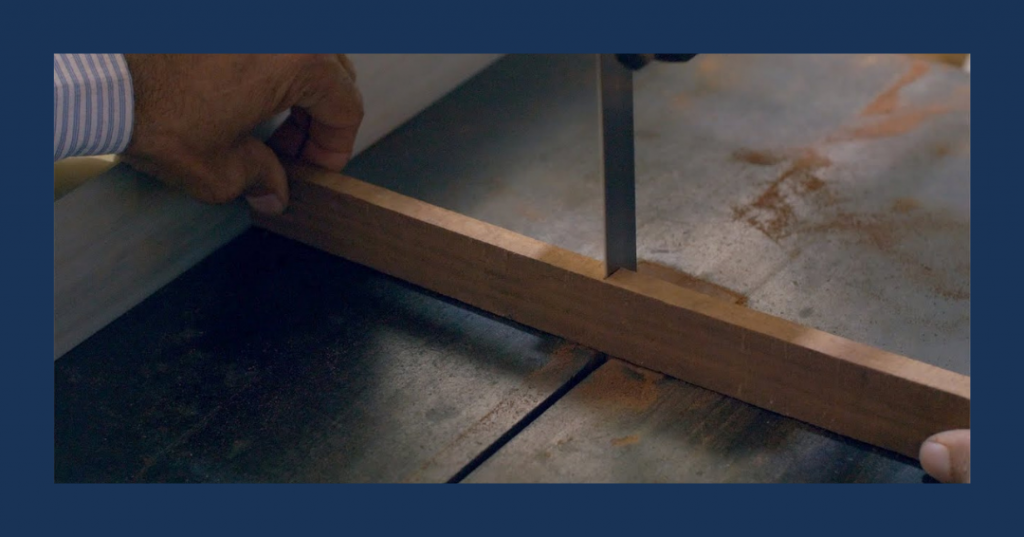
The seasoned wood is then cut to the required shape and dimension according to the product. Either, the wood is first cut and later inlaid, or inlaid first on different parts and cut later/
3. Preparation of the metal strips
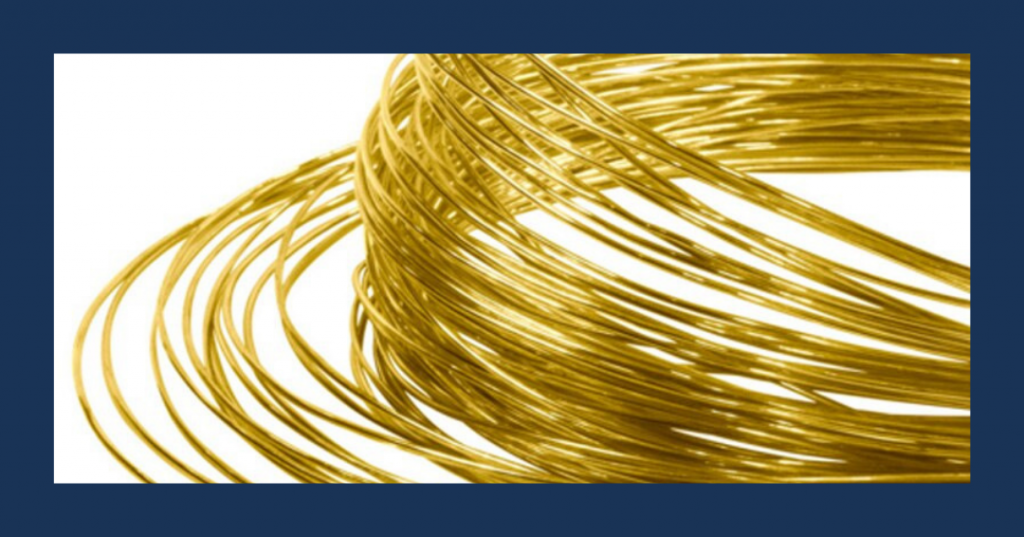
The marking of the strips inlayed is done on the sheet of metal. Approximately 1 inch wide strips are marked on the sheet of brass, copper, or silver. According to the marking, strips are cut out with the help of scissors. This cutting is done freehand without any marking. With the help of a hammer, one side of the edge is beaten to make it sharp. This side is cut with the help of scissors having a width of approx. 2 mm. These thin strips of wire are called as taar and used for inlay. The wires are further straightened with the help of a Chimti.
4. Marking
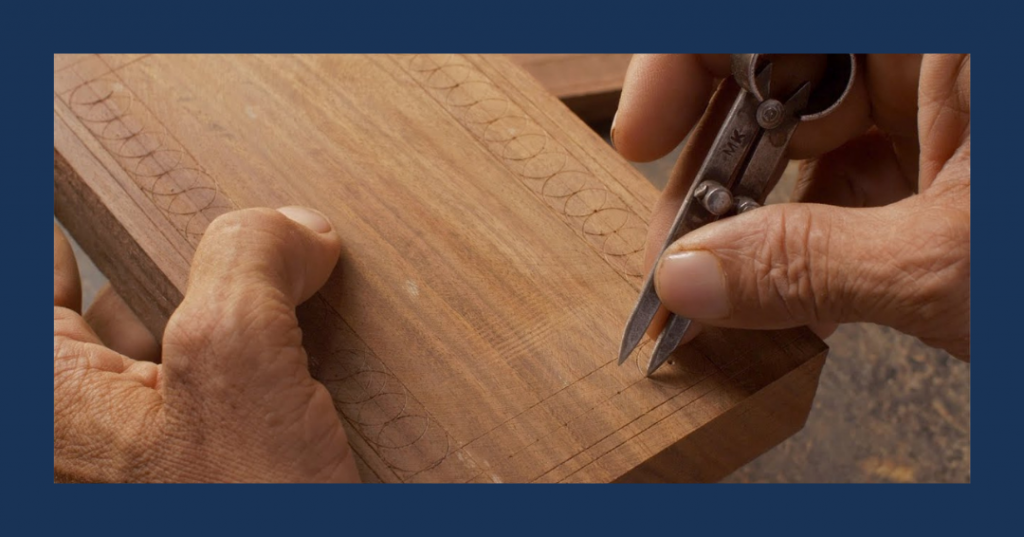
The design and pattern to be made on the product are either drawn directly or printed on a paper and pasted on the surface of the wood. The method changes according to the number of pieces or the shape of the product. Mainly the artisans draw the design by hand using a scale, compass, and right angle. The designs and patterns made are mainly in grids which are marked on wood with the help of marking tools. Parallel lines are drawn with the help of a marker and right angle. With the help of compass equal distances are marked and a grid is drawn. Once the grid is made the patterns are set in accordingly. Gunia and Prakaar are the D and compass respectively.
5. Engraving
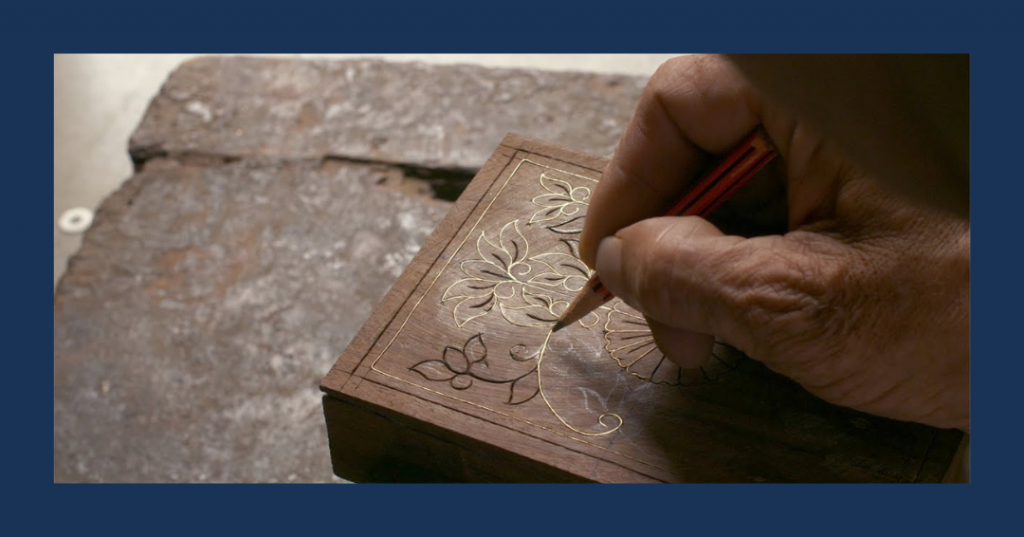
Then comes engraving after the layout and pattern making is done on the wood. The craftsman starts engraving the design with the help of a half-round chisel and hammer. The depth of engraving is around 1 mm which is less than the width of the prepared wire so that the wire fits in tightly. In the case of intricate designs, the entire pattern is not chiseled at one go. To prevent this, a small part of the design is chiseled. Then, the wire is inlaid and the process is repeated to complete the design pattern.
6. Inlaying
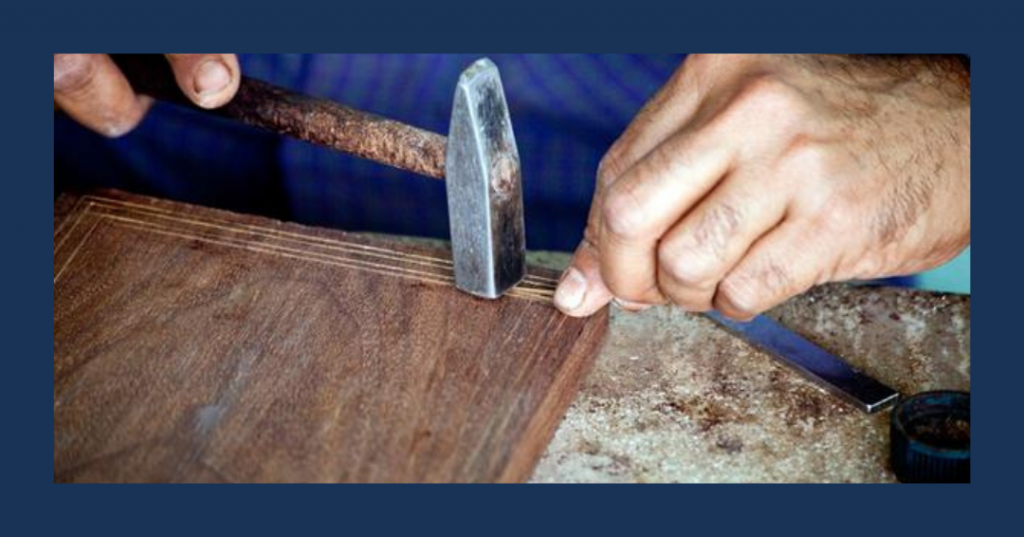
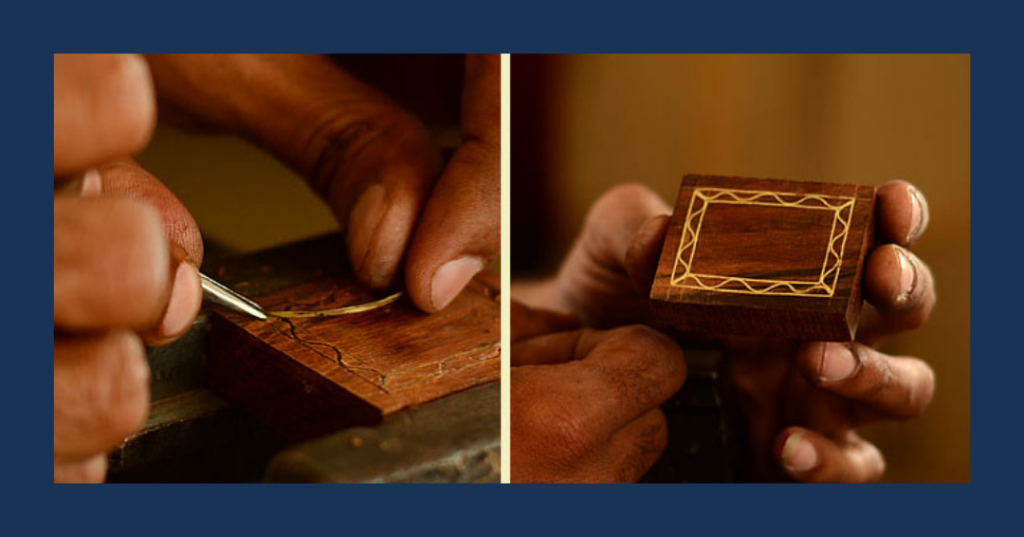
The artist then holds the wire is held and moves it with one hand along the contour of the design.He continues hammering with the another hand.The sharp edge of the wire is inlayed in the wood. The thick edge remains on the top. The excess wire is cut either with either a hammer or broken by twisting the wire in hand.
7. Leveling
The next step is to sand the product with Silli to make the surface even.
8. Filling
Burada is the sawdust of the same wood. It is mixed with fevicol and water. This mixture is applied all over the product with the help of a metal blade. The product is then kept in the sun for drying. This helps in filling the cracks, and spaces left while engraving or chipping the wood.
9. Scraping
After filling and drying the product, it is scraped with the blade to remove all the excess putti from the surfaces. Once the product is scraped 100 number sandpaper is used to rub the surface. This process is done to give the surface a smooth finish.
10. Buffing
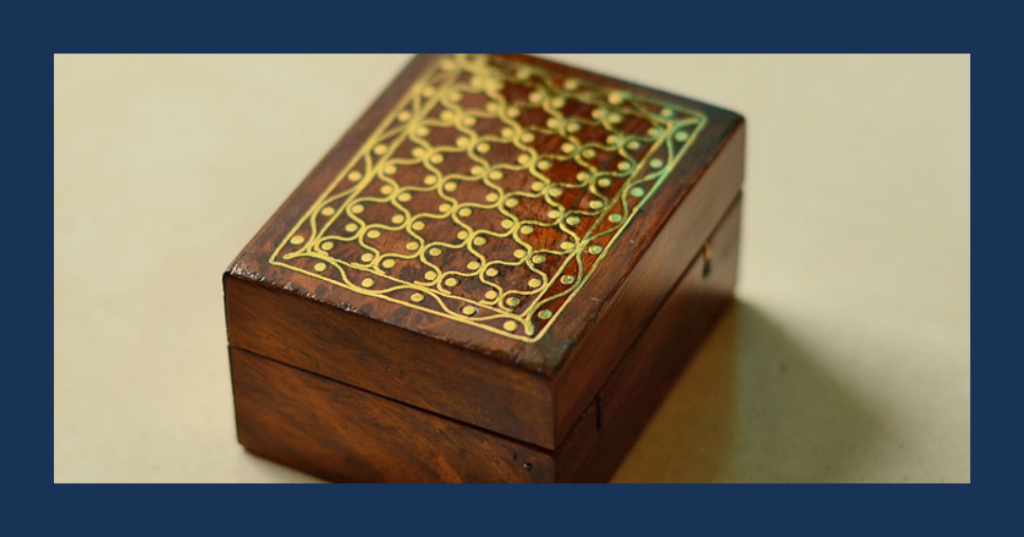
The product is, thus, given the final finishing by buffing. Buffing includes the use of two kinds of buff pads:
• Cutting pad (used to give a good finish)
• Shining pad (to give a lustrous look)
Once the product is buffed, it is rubbed with a cotton cloth containing wax polish. This not only saves the surface of the wood but also enhances the shine.
Follow Rajasthan Studio on Instagram for more amazing art and travel content. Reach out to us on email at contact[at]rajasthanstudio[dot]com. This blog is curated by Rajasthan Studio and written by Prathana Asiia.
.